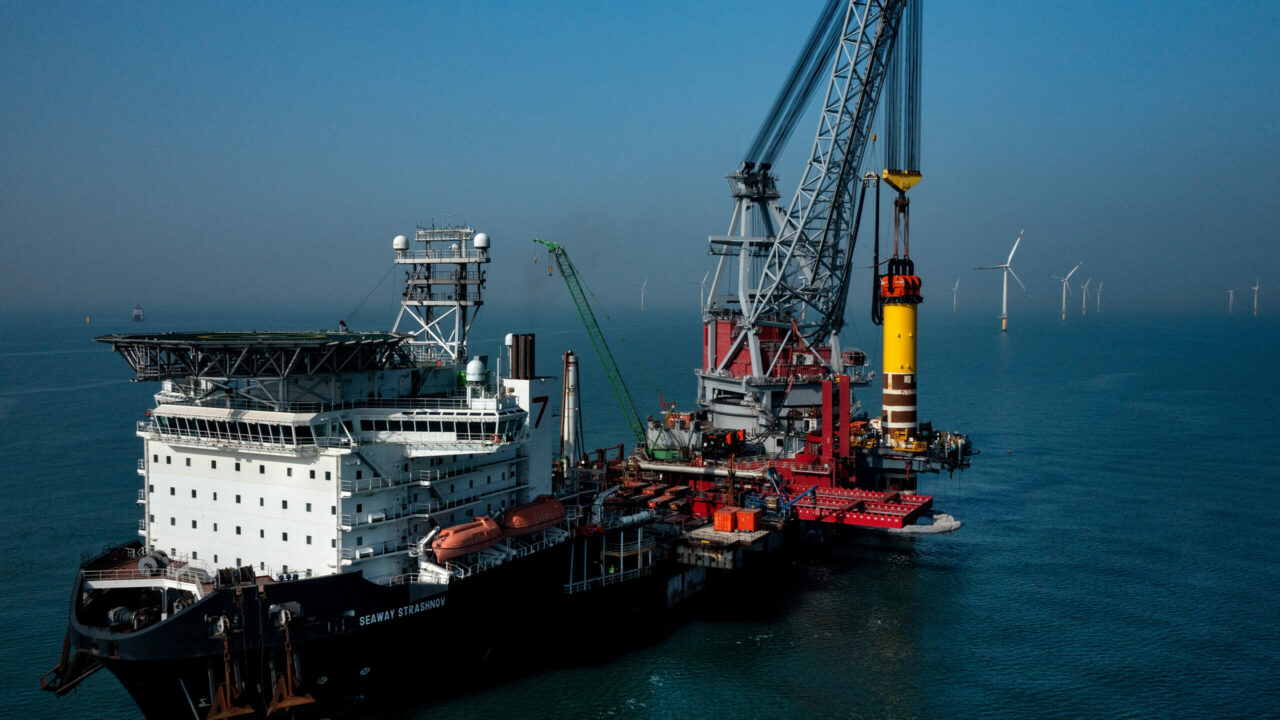
XXL
Monopile
installation
XXL MONOPILE INSTALLATION
The monopile has proven itself to be the most cost-effective foundation type for offshore Wind Turbine Generators (WTGs) with more than 80% of all the WTGs installed worldwide being installed on a monopile foundation.
In Europe alone, nearly 5,000 WTG monopiles were installed offshore by 2021. Although a few years ago it was expected that monopiles would no longer be used in water depths over 30 meter, ongoing development has shown that monopiles are now even being installed in water depths over 50 meter, which still offers a huge potential for this type of foundation.
However, the developments have also resulted in the WTGs becoming ever larger, with over 10MW units being installed already and talks of 20MW units in the not-too-distant future.
These larger WTGs also require larger monopiles, currently foreseen to become over 2,500 tons in weight, over 100 meter in length with diameters at the foot of more than 12 meter and at the top over 9 meter.
PILE INSTALLATION TOOLS
From a technical point of view, the ever-increasing top diameters of monopiles are causing the current standard installation method of using impact hammers to reach their limit. The anvil sizes simply can’t be enlarged sufficiently to have an effective energy transfer to drive these very large diameters piles to final penetration. With the increase in diameter the limits of the effectiveness of noise mitigation are being nearly reached already, which means the pressure of finding alternative installation methods is ever increasing.
THE SOLUTION
The CAPE VLT’s modular design makes it possible to scale up the tool to suit the pile dimensions which makes it basically not limited to a maximum diameter. The larger diameters make it possible to place more vibro units on the base frame interface between the vibro’s and the clamps. Top diameters up to 10 meters seem possible with the current configurations.
PILE INSTALLATION NOISE
The use of large impact hammers has a major downside, namely that they are very noisy and therefore damaging for the underwater wildlife. The noise emissions for impact driving increase as the piles become bigger. As these emissions are strictly regulated in many countries it is becoming increasingly more difficult to stay within the set limits.
Millions of Euro’s are being spent on Offshore Wind Farm projects in order to try and reduce the noise levels. Examples of mitigation measures are: bubble curtains, Hydro Dampers, Coverdams and other noise mitigation systems, used quite often in combination of them. Besides the huge costs involved these noise mitigation measures, they also add risk of stopping the works due to malfunctioning (parts) of the mitigation system, plus most systems require a lot of power to operate, increasing the environmental impact. The larger water depths decrease the effectiveness of the air bubble curtains due to the air bubbles drifting away with current and waves.
THE SOLUTION
Due to the inherently different method of driving the pile (reducing soils resistance and the pile penetrating by gravity rather than by hard blows) the noise emitted is far less than that of an impact hammer. Also the noise levels of the CAPE VLT are not directly related to the diameter of the pile, so XXL monopiles don’t automatically result in much higher noise emissions with vibro driving and it is expected that even with the large XXL monopiles that the noise levels will remain below the legally set levels.
PILE RUN
With the monopiles becoming bigger and the geographically use of monopiles growing as well, more locations with risk of pile run are met. Particularly locations with seismic activity seem to carry that risk. In China and Taiwan these risks have already shown that they should be taken seriously and in parts of US waters and even in the North Sea these risks should not be underestimated. The effects of a pile run can be severe in terms of likely damage to the vessel, pile and equipment as well as the likelihood of the monopile being out of installation tolerance.
THE SOLUTION
The CAPE VLT is physically connected to the pile and held by the crane and can therefore never be subject to a pile run. The worst that could happen is that the full weight of the pile and the CAPE VLT are hanging in the crane.
When installing in areas with risk of pile run, the installation methodology is such that most of the weight of the pile and the CAPE VLT are held in the crane, so only a transfer of a small part to the crane could occur instead of a shock load as in case of using an impact hammer, where the pile could also run uncontrollably and out of tolerance. Read more about pile run/drop fall here.
PILE INSTALLATION VESSELS
Most monopiles to date have been installed with either Jack-Up Vessels or floating vessels moored on anchors. Jack-Up Vessels have the advantage not to be affected by waves and current, providing a stable platform to work from which reduces the crane hook movements significantly and making more precision lifting possible. However due to having the legs penetrating the seabed, the effective crane load that can be utilised depends on the location and generally limits the maximum lifting capacity of a Jack-Up Vessel.
The current maximum crane capacities of the largest Jack-up Vessels are limited to about 2,000t. With XXL monopiles weighing already up to 2,500t or even more, this rules out the Jack-Up Vessels for XXL monopile installation. They are however perfectly suited for Wind Turbine Generator installation, and this is what they will be focusing on in the future.
For the XXL monopiles much larger cranes are required, which can be found on Heavy Lift Vessels and Semi Submersible Crane Vessels. These generally much larger vessels used to be moored on anchors for installation work which could take up to 8 hours per location, making them very uncompetitive for monopile installation work for the previous generation monopiles.
However with advances in Dynamic Position systems, the modern Heavy Lift Vessels and Semi Submersible Crane Vessels no longer need to use anchors, reducing the time on location significantly. However, the movements of the floating vessels do make it nearly impossible to keep a pile straight in a conventional gripper system whilst impact driving the pile on Dynamic Positioning. To resolve this problem, motion compensated grippers are being developed. Due to the high demand of installation vessels for XXL monopiles, many new floating vessels specifically designed for offshore wind installation have been and are being built.
THE SOLUTION
As the pile is connected to the CAPE VLT during upending, handling and driving, the installation vessel used will have to be equipped with a suitably large crane, which rules pretty much all Jack-Up vessels out of driving the XXL monopiles with the CAPE VLT.
As floating vessels are generally more expensive than jack-ups, the CAPE VLT gives the floating and Semi Submersible Crane Vessels a competitive edge. That leaves the Heavy Lift Vessels and Semi Submersible Crane Vessels, which are operating at Dynamic Positioning in combination with the CAPE VLT, the most efficient pile installation method. Even in case (some of) the piles would be required to be driven to final penetration with an impact hammer, as this could be done from a separate much smaller vessel when the monopile installation vessel has already left the location installing the next monopile.
PILE HANDLING
Not only the equipment for driving is challenged by the increasing sizes of the monopiles, also the handling equipment is meeting significant challenges. The impact hammer with the conventional installation method is placed loose on top of the pile, which means that until the pile has reached a stable penetration, it will need some sort of system to keep it from falling over and to keep it vertical during driving in order to meet the strict verticality tolerances. For Jack-Up Vessels such a gripper system can be static as the vessel is not moving in relation to the seafloor. However, a floating vessel on Dynamic Positioning requires a complex motion compensated gripper to keep the pile upright and vertical. With the increasing sizes in monopiles, these grippers will have to become bigger and more powerful as well. With the impact hammers becoming bigger and heavier, the side loads that the Dynamic Positioning system and motion compensated grippers have to deal with, grow even further, making it very hard to safely hold the pile upright and also reducing the weather windows.
THE SOLUTION
Heavy Lift Vessels and Semi Submersible Crane Vessels are generally more expensive vessels to operate but by operating on Dynamic Positioning, they become more competitive already and by optimizing the use of the CAPE VLT, a lot of time can be saved during the installation process. Free hanging installation brings even further benefits as it does not require a motion compensated gripper system, reducing handling time and risk of malfunctioning such complex gripper systems. The shortened installation period reduces the required operational weather window which increases productivity significantly. As the pile is fixed to the CAPE VLT and hanging in the crane, it can’t fall over, completely mitigating the risk of having to support a heavy pile with a loose impact hammer on top in a gripper system.
WHY USE THE CAPE VLT
FOR XXL MONOPILE INSTALLATION?
LOW NOISE LEVEL
UPENDING, LIFTING, DRIVING IN A SINGLE OPERATION
COMBINATION DYNAMIC POSITIONING – FASTEST METHOD
NO GRIPPER OR INSTALLATION FRAME
FAST
NO DIAMETER LIMITATION
vibro
lifting
technology
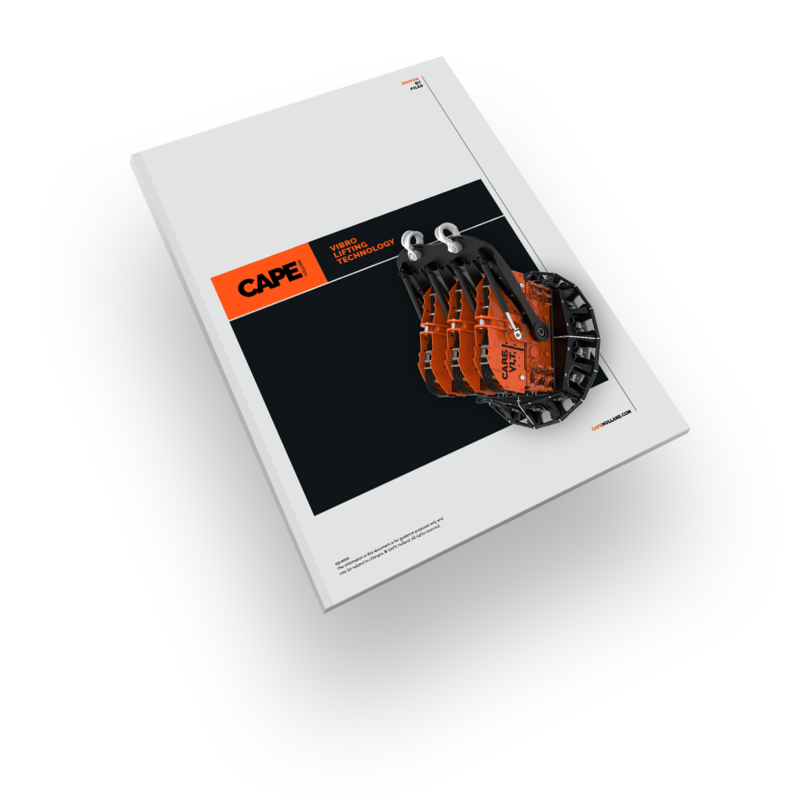
Discover how its unique features will uplift your next project; download the vibro lifting technology guide.